Gas leak in Vizag: A factsheet by Centre for Science and Environment
Styrene gas leaked from a Vizag factory called LG Polymers India Pvt Ltd. 11 people have died after inhaling the gas. This factsheet is based on the assessment done till 3.30 PM on May 7
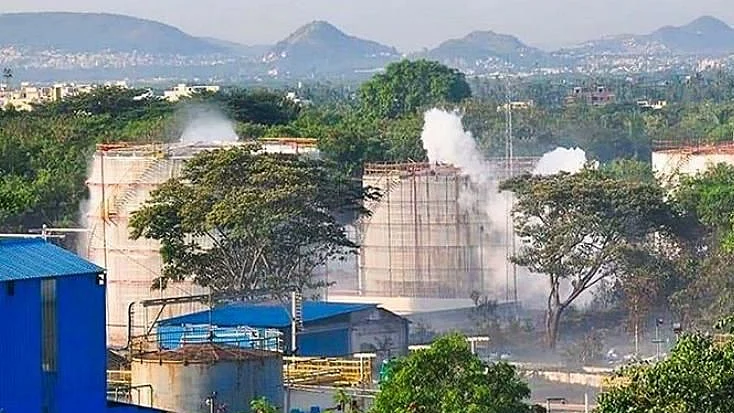
What happened?
Styrene gas leaked at 2.30 AM on May 7 from a Vizag (in the state of Andhra Pradesh in India)-based factory called LG Polymers India Pvt Ltd. Eleven people are reported dead after inhaling the gas.
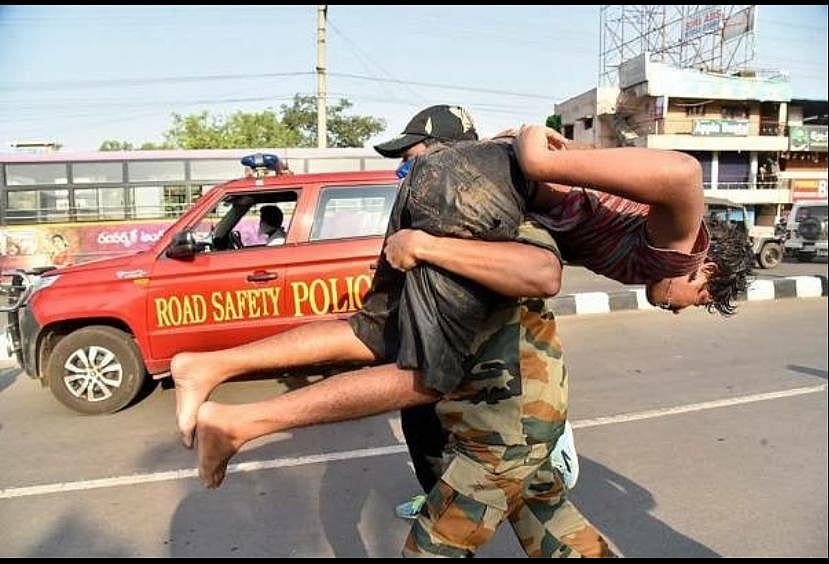
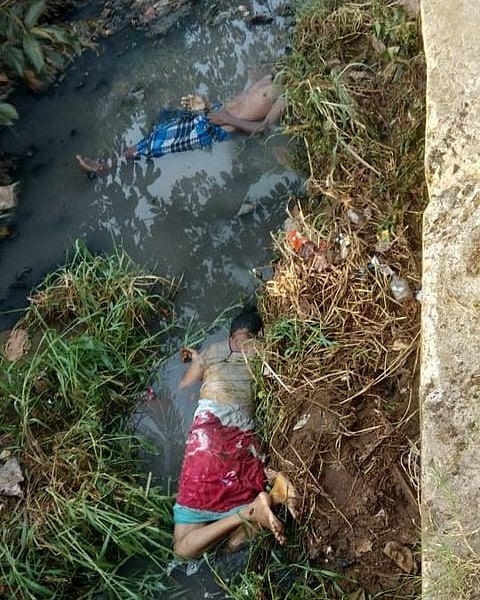
What is styrene? How toxic is it?
Styrene is an organic compound used in the manufacture of polymers/plastic/resins. It is manufactured in petrochemical refineries. It is a likely carcinogenic substance. It can react with oxygen in the air to mutate into styrene dioxide which is more lethal. According to India’s Manufacture, Storage and Import of Hazardous Chemical Rules 1989, styrene is classified as a ‘hazardous and toxic chemical’.
Acute (short-term) exposure to styrene in humans results in mucous membrane and eye irritation and gastrointestinal effects. Chronic (long-term) exposure results in impacts on the central nervous system (CNS), leading to headaches, fatigue, weakness, depression, CSN dysfunction, hearing loss, and peripheral neuropathy. If the amount of styrene goes beyond 800 ppm, then the person exposed to it can go into a coma.
The duration of the exposure and its relative concentration will determine toxicity – we currently know that roughly 3 tonnes of the gas leaked from its storage tank and the feeding line. We now need to determine exposure.
“Styrene can stay in the air for weeks. It is highly reactive, it can combine with oxygen to form styrene dioxide which is more lethal. The presence of other pollutants can also affect the reactivity. On a sudden note operating one reactor in full load can also lead to such disasters,” says Dr ThavaPalanisami, professor, Global Centre for Environmental Remediation (GCER) and CRC for Contamination Assessment and Remediation of the Environment (CRC CARE), University of Newcastle, Australia.
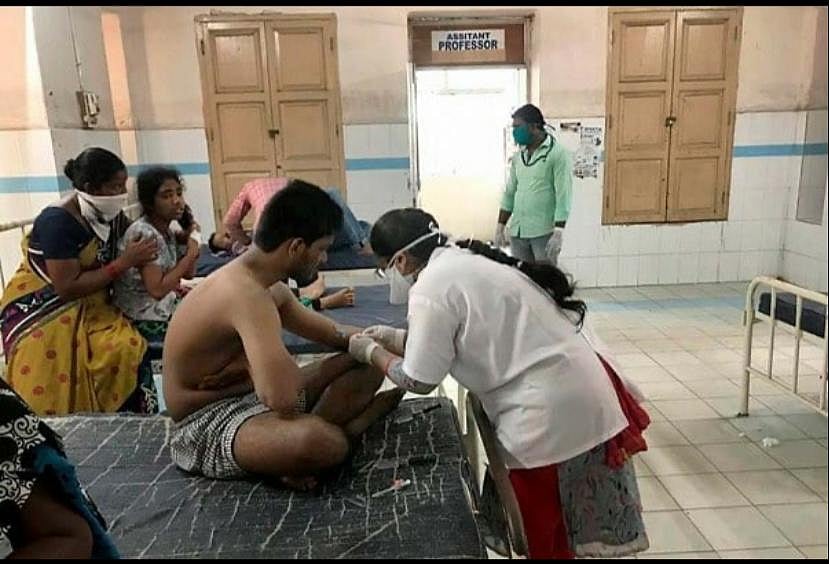
How did the disaster happen?
Styrene monomer was being used at the manufacturing plant to produce expandable plastics. The storage requirement of styrene monomer says that it should be stored strictly at a temperature below 17oC. There was a temporary partial shutdown of the plant owing to the COVID pandemic, excluding maintenance activities in the plant, which were being carried out as per a pre-determined schedule. The problem began as a result of styrene gas not being stored at the appropriate temperature. This caused pressure to build up in the storage chamber and led the valve to break, resulting in the gas leakage.
Also, the container that was being used to store styrene gas was old and not properly maintained. This non-maintenance of the facility resulted in the leakage of 3 tonnes of styrene into the surrounding areas.
Another issue was the defunct VOC detection system at the plant; there is no monitoring mechanism that was installed to specifically detect styrene. The facility is spread over 600 acres of land including the nearby residential areas (according to terms of reference submitted by the company in 2018, it is spread over 231 acres). The impact zone has been in the range of 2-3 km. There is a revenue village nearby and the facility is surrounded by residential areas, resulting in a higher rate of exposure.
The most important immediate treatment is to give oxygen to the affected people. The people in the zone also need to be evacuated as long-term exposure can be detrimental to their health. Also, as styrene reacts to form styrene dioxide, the air could remain contaminated for some time. However, the winds blowing from the sea could also help to disperse the gas.
In 2018, the factory hadsubmitted a ₹ 168 croreproposal to the Union Ministry of Environment, Forest and Climate Change to expand its production capacity by another 250 tonnes per day (tpd) from the current 415 tpd. This permission, as we understand it, has been recently granted.
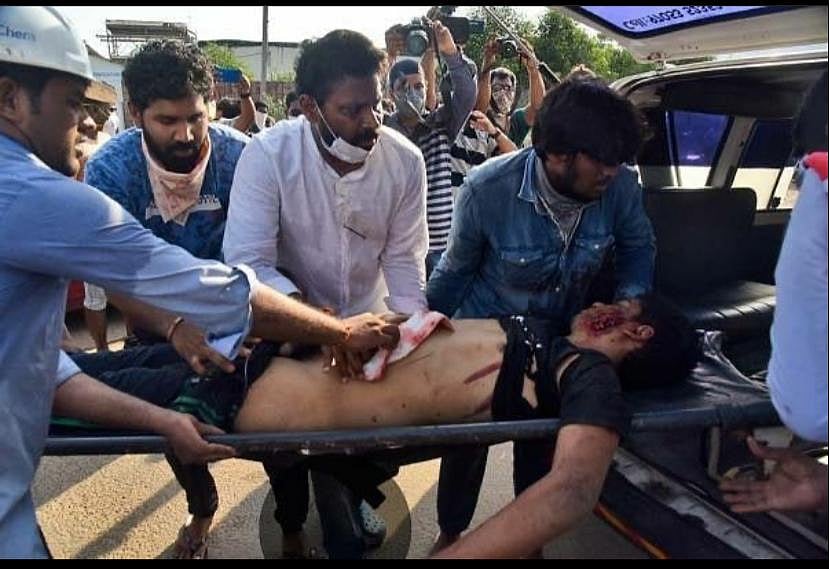
Post-Bhopal disaster, there are clear guidelines on storage of hazardous chemicals in plants -- what are these?
After the Bhopal disaster, many legislations were enacted beginning with the Environment (Protection) Act, 1986 to the Public Liability Insurance Act, 1991. According to The Manufacture, Storage and Import of Hazardous Chemical Rules, 1989, styrene is classified as a ‘hazardous and toxic chemical’.
- Environment (Protection) Act, 1986: Omnibus act that gives sweeping powers to the Central government to take all measures to protect the environment. Under it are the following Rules:
- Environment (Protection) Rules, 1986: Set discharge and product standards – source standards for restricting pollution; product standards for manufactured goods and ambient air and water standards – for regulating quality of life and environmental protection.
- Hazardous Waste (management, handling and trans-boundary movement) Rules, 1989: Industry required to identify major accident hazards, take preventive measures and submit a report to the designated authorities.
- Manufacture, Storage and Import of Hazardous Chemicals Rules, 1989: Importer must furnish complete product safety information to the competent authority and must transport imported chemicals in accordance with the amended rules.
- Chemical Accidents (Emergency, Planning, Preparedness and Response) Rules, 1996: Centre is required to constitute a central crisis group for management of chemical accidents; set up quick response mechanism termed as the crisis alert system. Each state is required to set up a crisis group and report on its work.
- Factories Amendment Act, 1987: Provision to regulate siting of hazardous units; safety of workers and nearby residents and mandates for on-site emergency plans and disaster control measures.
- Public Liability Insurance Act, 1991: Imposes a no-fault liability on the owner of hazardous substance and requires the owner to compensate victims of accident irrespective of any neglect or default. For this, the owner is required to take out an insurance policy covering potential liability from any accident.
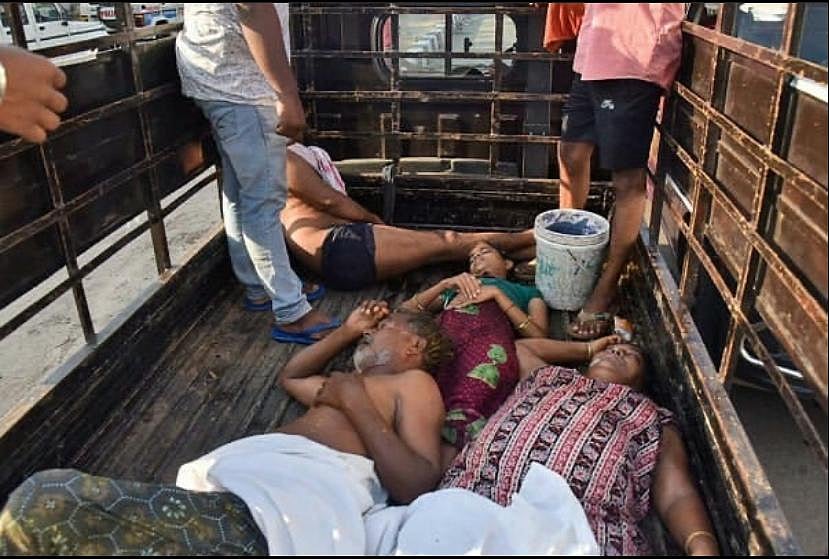
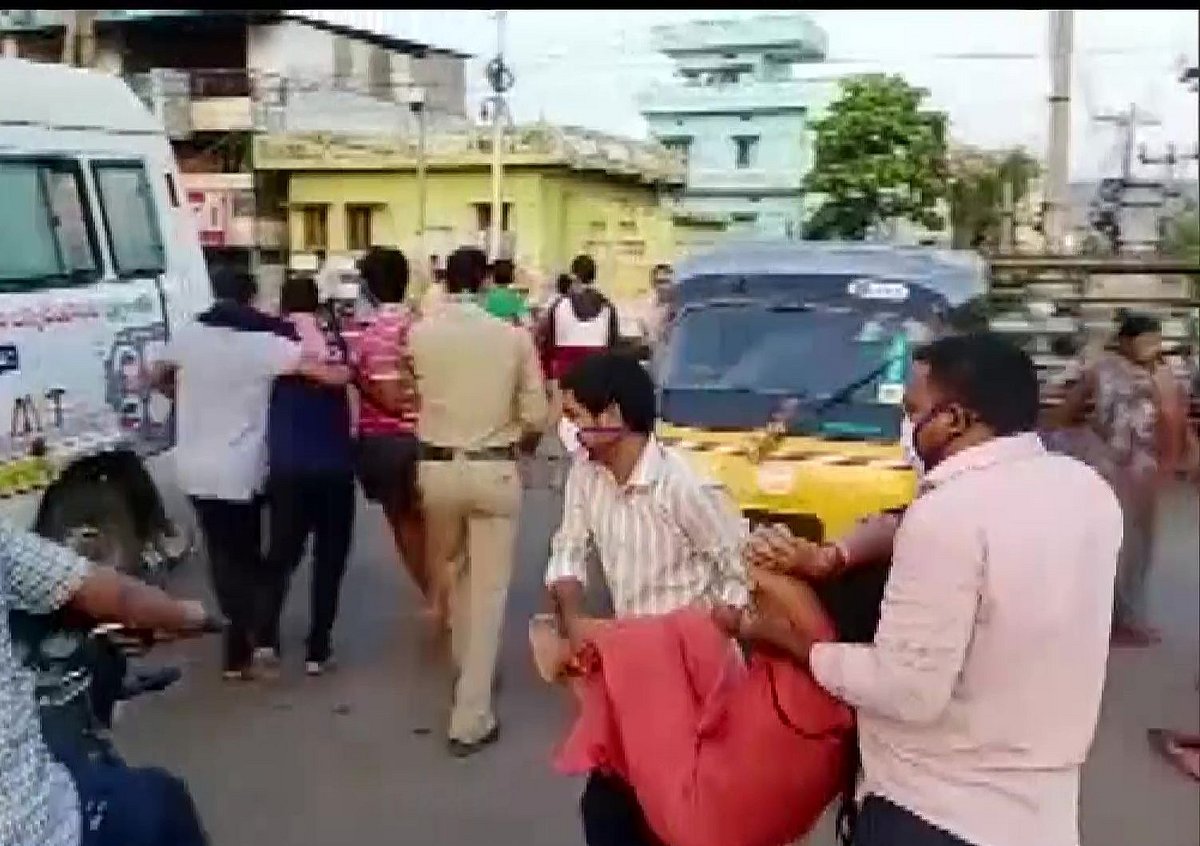
Did the company not follow the stipulated rules for storage and handling of hazardous chemicals?
There are clear rules on hazardous chemical storage under the EPA, 1986.The unit in question is an ISO-certified facility, which means it has a protocol for everything.
However, what seems to be the case is that the plant management, in its haste to re-start the plant,ignored the protocol of doing maintenance of the plant before resuming operations. This, combined with the lack of proper storage of the gas – not maintained at the temperature required – and faulty fixtures could have resulted in the accident.
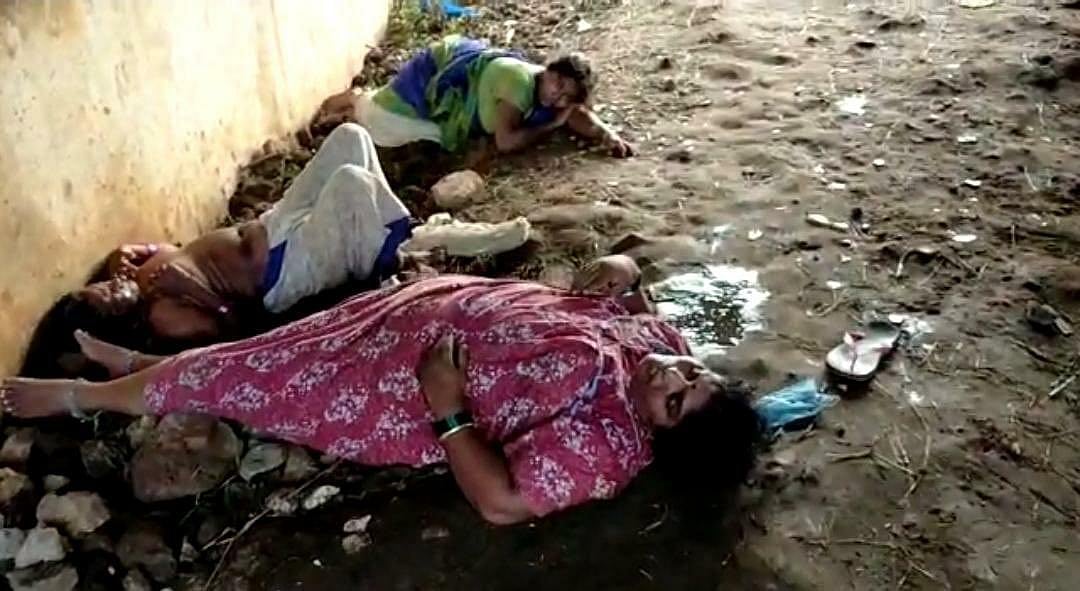
The lesson for COVID times -- Vizag could be just a tip of the iceberg
This shows us that there are ticking bombs out there as the lockdown ends and industries start resuming activities. Therefore, an immediate directive must go to all units to ensure safety while resuming operations -- in case the lockdown continues, these safety precautions must not be negated.
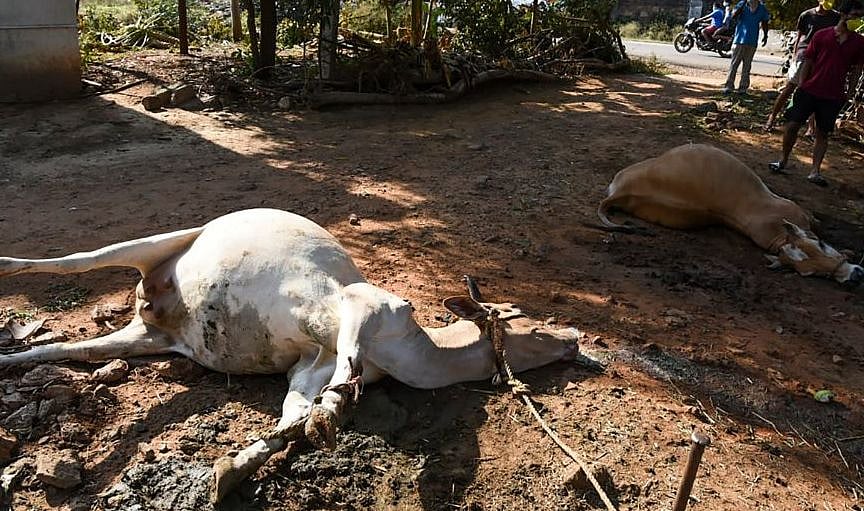
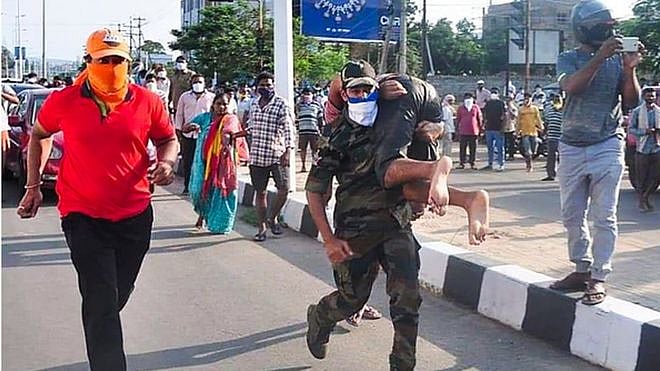
Follow us on: Facebook, Twitter, Google News, Instagram
Join our official telegram channel (@nationalherald) and stay updated with the latest headlines