IIT researchers develop indigenous Metal 3D printers for defence, aerospace and general engineering sectors
3D printing is a more agile process than other fabrication methods and allows manufacturers to go from design to complex metal parts faster, easier, and at lower costs
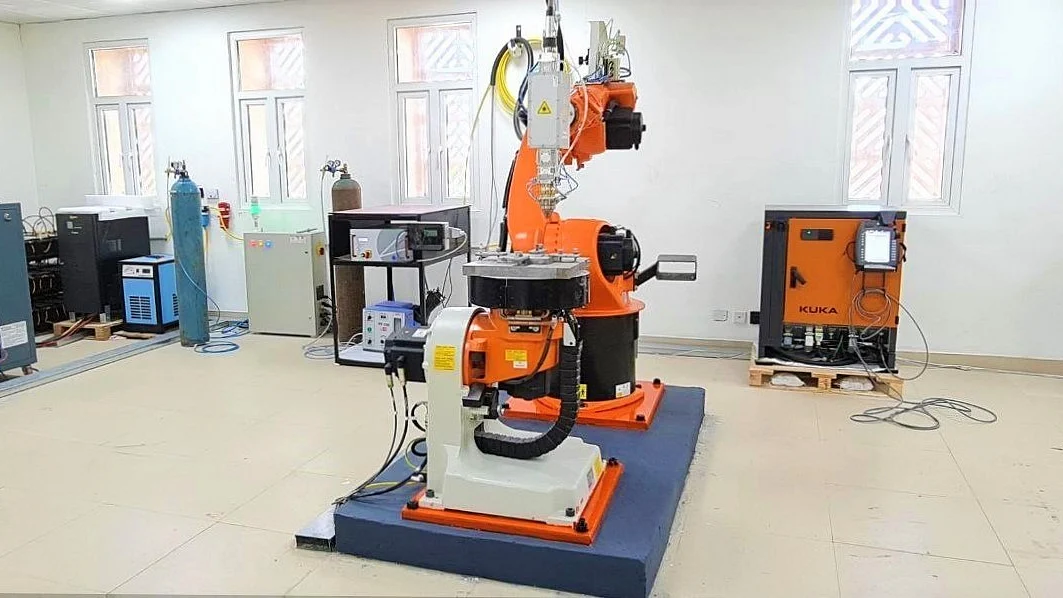
India’s 3D metal printing capabilities have got a shot in the arm with researchers at IIT Jodhpur developing an indigenous printer based on the Direct Energy Deposition (DED) technology.
Developed under a project whose main objective is to reduce the cost of Metal 3D printers and attract a broader range of users, all components of the developed printer, except the laser and robot systems, are designed and manufactured in India.
Implementing Metal 3D printing correctly can greatly improve business efficiency and agility by either eliminating the need for detailed drawings and machine programming or drastically shortening lead times that bog down product development processes.
However, despite the fact that Metal 3D printing technology was introduced a few years after the launch of Polymer 3D printing, it is yet to experience the tremendous growth that the Polymer 3D industry has achieved, especially in India.
The high price of the product and the more expensive proprietary metal powders imported from abroad are some of the reasons for the limited growth of Metal 3D printers. The printer developed is suitable for repairing and adding additional material to existing components. It is therefore believed to be ideal for printing fully functional parts for a range of industries, like aerospace, defence, automotive, oil and gas, and general engineering, to name a few.
Dr. Ravi K. R., Associate Professor, Department of Metallurgical and Materials Engineering, IIT Jodhpur, said, "The small success of this research has given great hope to our team to undertake new endeavours. Moreover, it will further strengthen the trust placed on our team and organization by the funding agencies and industry that are assisting our current research and will be assisting us in the future."
Besides Dr. Ravi, the research team from IIT Jodhpur involved in this project are Dr.V. Narayanan, Associate Professor, Department of Physics, Dr. Abir Bhattacharyya, Assistant Professor, Department of Metallurgical and Materials Engineering, Dr. Sumit Kalra, Assistant Professor, Department of Computer Science and Engineering, Dr. Rahul Chhibber, Associate Professor, Department of Mechanical Engineering, and Dr. Hardik Kothadia, Assistant Professor, Department of Mechanical Engineering.
"Our study results show that if all the parts needed to make a metal printing machine could be manufactured indigenously, the cost of a Metal 3D printing machine could be reduced by two to three times. Moreover, such an initiative would further strengthen the policy decisions of the Government of India under the ‘Atmanirbhar Bharat’ initiative,” Dr. Ravi said.
3D printing has changed the landscape of manufacturing the world over. It is a more agile process than other fabrication methods and allows manufacturers to go from design to complex metal parts faster, easier, and at lower costs.
This machine developed by researchers at IIT Jodhpur can print 3D parts with metal powders that are made in India.
In addition, India's first state-of-the-art variable spot size laser optics without compromising on laser beam homogeneity for laser cladding and additive manufacturing process is available in this machine.
The team at IIT Jodhpur has developed this machine's tool path planning software and coaxial nozzle. It also has in-situ monitoring technologies which constantly monitor the melt pool temperature and clad thickness during the additive manufacturing process.
Follow us on: Facebook, Twitter, Google News, Instagram
Join our official telegram channel (@nationalherald) and stay updated with the latest headlines